Newsroom
Experten-Interview: Alternativen zu Stahl für den Verschleißschutz in Förderanlagen
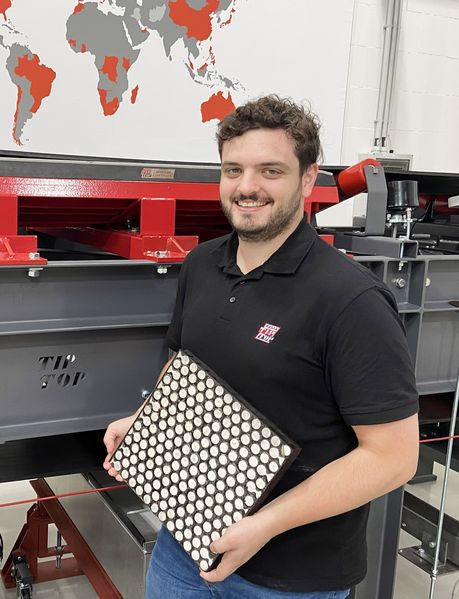
Poing bei München, 26. September 2023. Stahl gilt als Material der Wahl, um Oberflächen in Förderanlagen für schwere Materialien gegen Verschleiß zu schützen. In der Praxis stößt Stahl jedoch in vielen Fällen an seine Grenzen. Rico Harting, Produktmanager bei REMA TIP TOP entwickelt seit vielen Jahren Lösungen für den effizienten und nachhaltigen Verschleißschutz in Förderanlagen. Im Interview erklärt er, welche alternativen Materialien für den Verschleißschutz in Frage kommen und wie moderne Verbundsysteme wie REMALOX HD dabei helfen, Instandsetzungs- und Wartungskosten zu reduzieren und Standzeiten deutlich zu erhöhen.
Welches sind besondere Herausforderungen bei der Förderung schwerer Materialien?
Es ist kein Geheimnis, dass schwere oder scharfkantige Fördergüter wie Steine und Erze abrasiver sind als leichte oder runde Materialien. Deshalb kann es entlang des gesamten Förderweges zu erhöhtem Verschleiß kommen. Besonders kritisch sind Aufund Übergabestellen, wo das schwere Material beispielsweise von einem Förderband in einen Trichter oder auf eine Rutsche übertragen wird. Je nach Fördergeschwindigkeit, Fallhöhe und Aufprallwinkel kann hier der Verschleiß an den Oberflächen von Komponenten besonders hoch sein. Das treibt die Instandhaltungsund Wartungskosten nach oben und reduziert die Standzeiten einer Anlage. Manche Firmen müssen den Betrieb ihrer Förderanlage mehrmals im Jahr unterbrechen, um den Verschleißschutz an kritischen Stellen instand zu setzen.
Welche Rolle spielt Stahl beim Schutz vor Verschleiß in der Fördertechnik heute?
Stahl gilt ohne Zweifel als Material der Wahl, um die Oberflächen von Vibrationsförderern, Zyklonen, Rutschen, Verladestellen, Trichtern etc. gegen Verschleiß durch schweres Fördergut zu schützen. Dabei kommen in der Regel Platten, Bleche und Leisten zum Einsatz, die je nach Belastung mit verschleißfesten Stahllegierungen ausgestattet sind. Bei mittelschweren bis schweren Anwendungen im Bergbau und in Steinbrüchen, aber auch in Goldminen ist Stahl für die Verkleidung von Oberflächen sehr verbreitet, obwohl Stahl im Einzelfall nicht immer die optimale Lösung ist. Häufig setzen Betreiber auf Stahl, obwohl leichtere Lösungen aus Gummi besser geeignet wären. Andere halten am Stahl fest, obwohl er den hohen Anforderungen nicht gerecht wird.
Wo stößt Stahl beim Verschleißschutz an seine Grenzen?
Obwohl Stahl eine wichtige Rolle beim Verschleißschutz in der Förderung schwerer Materialien spielt, gibt es Anwendungsszenarien, in denen Stahl an seine Grenzen stößt und andere Verschleißschutz-Technologien zu besseren Ergebnissen führen. Bei der Förderung von hochabrasiven Materialien kann selbst hochverschleißfester Stahl mit der Zeit stark abgenutzt werden. Kanten werden aufgerissen oder es entstehen Ermüdungsrisse durch Stoßbelastung. Zudem kann Stahl unter extremen Bedingungen – beispielsweise durch Feuchtigkeit, Hitze und Säure – korrodieren. Und wer einmal erlebt hat, wie Eisenerz aus großer Höhe in einen Trichter mit Stahlauskleidung stürzt, kann bestätigen, dass Stahl nicht gerade zum Lärmschutz in Anlagen beiträgt. Hier eignen sich andere Materialien oder Verbundsysteme oft besser.
Welche Alternativen zum Verschleißschutz mit Stahl gibt es?
Als Alternativen zum Stahl kommen für den Verschleißschutz in Förderanlagen grundsätzlich Gummi, Keramik und Verbundsysteme aus diesen beiden Materialien in Betracht. Gummi hat den Vorteil, dass es den Aufprall von Fördergut elastisch kompensieren kann, was unter anderem den Lärm in der Anlage deutlich reduziert. Allerdings ist Gummi für schweres Fördergut nur bedingt geeignet. Eine bessere Alternative ist hier der Verschleißschutz aus Keramikplatten und -komponenten, die sehr widerstandsfähig sind. Allerdings ist Keramik relativ spröde, was kein Problem ist, wenn schweres Material über die Oberfläche gleitet oder rollt. Kritisch wird es allerdings, wenn das Fördergut aus großer Höhe senkrecht auf die Keramikoberfläche aufprallt. Dann können Oberflächen brechen und Kanten abplatzen.
Was raten Sie Unternehmen, die ihren Verschleißschutz verbessern wollen?
Es lohnt sich, über den Tellerrand von Stahl, Gummi und Keramik hinwegzusehen und neue Konzepte in den Blick zu nehmen. Verbundsysteme wie REMALOX HD kombinieren die Stärken von Gummi und Keramik und ermöglichen so einen langlebigen und wirtschaftlichen Verschleißschutz. Bei REMALOX HD absorbiert eine Gummimatrix die Prallenergie, während einvulkanisierte Keramikelemente vor Verschleiß schützen. Ein Unterboden aus Metall ermöglicht die unkomplizierte Schraubverbindung auf den Einsatzflächen. Besonders bewährt hat sich REMALOX HD in Anlagen mit großen Fördermengen von gebrochenem Material, langen Instandhaltungsintervallen von 12-15 Monaten und baulich ungünstigen Aufprallwinkeln, wo Keramik allein für einen robusten Verschleißschutz nicht geeignet ist.